How we deal with cooling products
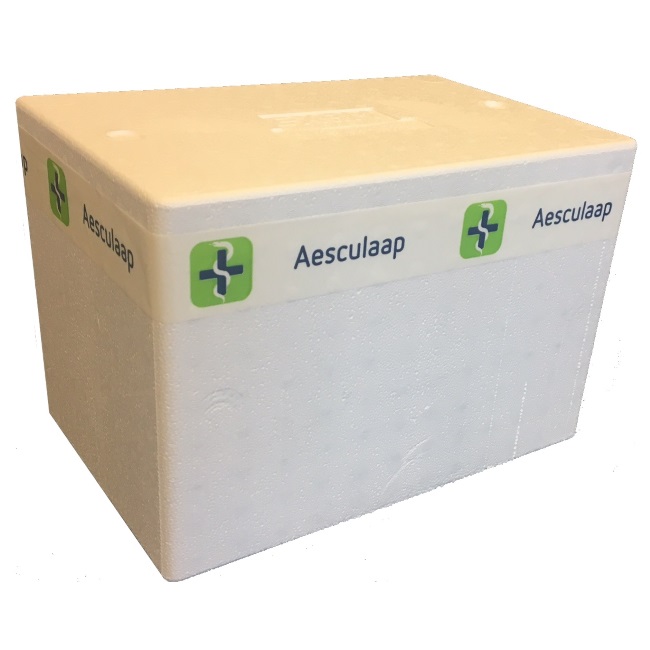
23/09/2021
Aesculaap has been GDP certified for many years, which means that our logistics process complies with European standards for Good Distribution Practices. This means that we can guarantee the quality of our products, from manufacturer to you as a customer. The logistics process of our refrigeration products is a profession in its own right. Are you curious about how we pack and distribute our refrigeration products? Then read on quickly!
We pack and distribute cooling products as follows:
- Cooling products (2-8°C) are packed in cool boxes. Our cool boxes are made of polystyrene foam, this material ensures optimal insulation;
- We store the cool boxes in our fridge, so that the cool boxes are also pre-cooled;
- In the refrigerator, the cool boxes are filled with cooling products, so that the cooling products are not exposed to a higher temperature;
- Cooling elements (-21°C) are then added to the cool boxes, which maintain the temperature;
- The cool boxes are closed, after which the lids are sucked in and leakage is prevented;
- The lids are additionally secured with tape, so that they cannot come loose from the cool boxes;
- The cool boxes with cooling products and cooling elements are no longer opened after leaving the refrigerator;
- The filled cool boxes are normally delivered within 24 hours by our carrier (who is also GDP certified), so that the quality of the cooling products is guaranteed;
- If you are not present at your practice when our transporter offers the cooling products to you and/or the products cannot be placed directly in your refrigerator, the cooling products will also remain at the right temperature thanks to the way they are packed!